فلاش ها و درایر ها در صنعت چاپ تیشرت
خشک کن فلاش Flash Dryer
استفاده از رنگ های پلاستیسول نیاز به داشتن خشک کن های سریع و کار آمد را بیش از پیش جهت واحد های چاپ پوشاک نمایان ساخت ودر الویت دستور ساخت تولید کنندگان تجهیزات چاپ تیشرت قرار گرفت.در واقع فلاش ها یک خشک کن میانی اتوماتیک جهت چاپ پارچه وپوشاک در مدل های مختلف (وابسته به ابعاد خشک کردن )

انواع فلاش های تولید شده به شرح زیر می باشد.
- بلاک فلاش IR Lang-Wave
- فلاش گازی با پد گازی
- فلاش IR Short-Wave
- فلاش IR Medium-Wave
موارد مشترک بین فلاش ها ی تولید شده با لامپ های Quartz IR
- قابلیت تنظیم ارتفاع
- دارای قابلیت حرکت وتراز شدن
- مناسب جهت قرار گرفتن در بین ایستگاه های ماشین چاپ اتوماتیک ودستی
- دارای تایمر
- دارای کلید جداگانه جهت هر لامپ
- دارای میکرو سویچ های نوری و مکانیکی
بلاک فلاش IR Lang-Wave
که به جرعت می توان گفت که از نسل اول فلاش ها می باشد همانطور که از نام آن مشخص است از نوع المنت لانگ ویو که گرم شدن آن نیاز به زمان دارد که در عمل دائم روشن می باشد بدون تایمر و بدون فن .همچنین جهت میزهای چاپ دستی خود فلاش حول محور پایه بشکل دستی می چرخد که پس از خشک شدن چاپ از روی سطح پالت کنار رفته که باعث سوختن چاپ وپارچه نشود ودر نوع مناسب جهت ماشین های اتوماتیک بشکل اتوماتیک از سطح پالت کنار می رود.بزرگترین اشکال مصرف برق زیاد به جهت دائم روشن بودن و خطر سوختن وآتش سوزی است.
فلاش گازی با پد گازی
در سایر موارد مانند بلاک فلاش است و تفاوت فقط در نوع انرژی مصرفی است.
فلاش IR Short-Wave
ترکیبی از لامپ های Quartz IR وهوادهی جهت افزایش راندمان مناسب جهت رنگ های پلاستیسول و پایه آب و به جهت داشتن کلید های جداگانه جهت هر لامپ می توان فقط سطح مورد
نیازرا خشک کرد و از اتلاف انرژی جلوگیری کرد و به جرعت باید گفت بیشترین مدل فلاش تولید شده می باشد .و به دلیل داشتن میکرو سویچ وتایمر فقط در زمان تعیین شده روشن و خاموش
می شود وهیچگونه نگرانی از بابت سوختن وآسیب به پالت و پارچه وجود ندارد و نسبت به نوع بلک فلاش مصرف کم انرژی آن توجیه اقتصادی دارد
فلاش IR Medium-Wave
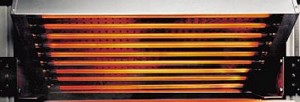
نوع جدید لامپ های طراحی شده با مصرف انرژی کمتر و سرعت خشک کردن سریعتر ونوع سنسور دار آن معروف به نوع مجیک یا هوشمند است که با تنظیم دما برای ماشین های اتوماتیک بهترین گزینه می باشد.
فرایند تکمیل و تثبیت چاپ پارچه بشرح زیر می باشد:
دما و زمان مورد نیاز جهت تکمیل و تثبیت رنگهای مورد مصرف معمولا از سوی تولید کننده گان رنگ در دستورالعمل مصرف رنگ اعلان میگردد
ولی چاپگرهای با تجربه با توجه به نوع پارچه و ایجاد جلوهای ویژه در آن تغییراتی را لحاظ میکنند
جهت تکمیل وتثبیت انواع چاپهای پارچه به دماهایی از 120 درجه سانتگراد تا 220 درجه و زمان 10 ثانیه تا 3 دقیقه و بیشترمورد نیاز میباشد.که پس از تکمیل وتثبیت تست شستشو معرف عملکرد صحیح میباشد.
تست شستشو10 بار شستشوی کامل با دما مناسب با مقاومت پارچه در ماشین لباسشویی و شوینده های خانگی می باشد
درایرDryer
درایرها شامل اتاق های حرارتی و درایر های نقاله ای:
ذکر این نکته ضروری می باشد که کارگاه های چاپ تی شرت در ایران در ابتدا هیچگونه تجهیزاتی را جهت تکمیل وتثبیت پارچه را در اختیار نداشتند وبیشتر از رنگ وموادی استفاده می کردند که هوا خشک بوده و نیاز به پخت نداشته باشند اما آمدن رنگهای جدید به ویژه پلاستیسول و رسیدن به کیفیت های بهتر نیاز به داشتن درایر را جهت کارگاهها الزامی کرد.

کارهای چاپ شده فقط تا مرحله خشک شدن در روی طناب های میز های چاپ قرار می گرفتند.وپس از آن تحویل واحد های تولید پوشاک می شدند و حداکثر در مرحله اتو کاری کمی حرارت میدیدند.
ابتدا جهت تکمیل و تثبیت تیشرت های چاپ شده از اتاقک های ثابت و سیارحرارتی سیرکوله دار (دارای گردش هوا) استفاده میشد روش کار بدین گونه بود که تیشرت های چاپ شده را د رقفسه هایی قرار میدادند و انها را داخل اتاقک می گذاشتند سپس پس از بستن درب اتاقک منبع حرارتی را که برقی ویا گاز یاگازوئیل بود را روشن میکردند و پس از رسیدن به دمای مورد نظر عملیات تکمیل به پایان می رسید .
معایب : پهن کردن وجمع کردن کارها که بسیار وقت گیربوده وطی چند مرحله انجام می گردیده همچنین تفاوت طبقات بالا وپایین از نظر اختلاف دما در نتیجه عدم کیفیت مناسب در پخت بطوریکه طبقات بالا چون حرارت بیشتری از طبقات پایین داشته اند .

درایرهای نقاله ای شامل :
- المنتی IR میله ای و صفحه ای
- لامپ های IR تابشی و حرارتی
- هوای گرم IR و یا گازی
امروزه تقریبا کلیه درایر های تولید شده در چند چیز مشترک میباشند
1-استفاده از نقاله های تفلونی توری MM4x4 و مقاوم تا 250 درجه سانتی گراد
2-کلید تنظیم سرعت نقاله
3- سیستم کنترل لغزش نوار نقاله
4-گردش هوا (سیرکوله)
5-اگزوز جهت خروج بخارات و دود حاصل از پخت رنگ
6-صفحه نمایش دما
7-تظیمات کشش توری
سیر تغییرات در ساخت درایر
پس از مشاهده اشکالات درایر های اتاقکی کلیه درایر های تولید شده شکل امروزی را داشته و بشکل نقاله ای (کانتینیوز) می باشند.
1-ابتدا در ساخت درایرهای نقاله ای از المنت های میله ای و صفحه ای ساده و IR همراه با گردش هوا و تنظیم ارتفاع منبع حرارتی از سوی تولید کننده گان در دستور کار قرار گرفت
اما پس ازمدتی که از عملکرد این نوع درایرها گذشت ایراداتی که در مورد استفاده از این نوع درایر در واحد های تولیدی ثبت گردید که به شرح زیر می باشد .
- تغییر رنگ پارچه ها در سرعت های پایین
- سوختن تولیدات دوخته شده در سرعت های پایین
- عدم خروجی یکدست در مورد رنگ های خاص در سرعت های پایین
- عدم دمای یک نواخت در سطح حرارتی

اشکالات به وجود آمده در مورد این نوع درایر ها باعث گردید که بعضی از تولیدکننده گان به فکر استفاده از یک پوشش شیشه ای در اطراف المنت ها جهت جلو گیری از بروز ایرادات بوجود آمده در مورد درایر های المنتی گردید که باعث بوجود آمدن المنت های بشکل لامپ های میله ای گردید.
2-بدین روش درایرهایی با لامپ های میله ای پا به عرصه تولید گذاشتند حتی بعضی از تولید کننده گان از نوعی ذره بین به عنوان پوشش شیشه ای در اطراف المنت ها هم استفاده کردند ولی این نوع پوشش ها هم نتوانست ایرادات ناشی ازتابش مستقیم المنت و تغییر رنگ پارچه را کاملا بر طرف سازد .
با استفاده از تجارب گذشته وتست های آزمایشگاهی وبررسی عملکرد درایر های گازی یا گازوئیلی کاملا این نکته مشهود گردید که درایر هایی که از روش هوای گرم استفاده میکنند ومنبع حرارتی مستقیما با سطح پارچه در ارتباط نمی باشد بهترین روش بوده که باعث بوجود آمدن درایر های برقی با روش تولید حرارت به روش درایر های گازی ودیگر سوخت های فسیلی شد که روش کار تولید حرارت دورتر از سطح پارچه وانتقال آن به سطح پارچه به روش وزیدن که موجب تولید درایر های به روش های Air Jet وTurbo Jet گردید.
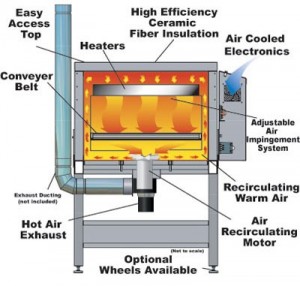
در این روش حتی با سرعت های کم نیز تغییراتی در رنگ های پارچه ها به وجود نمی آید وبهترین روش ساخت درایر می باشد.
اما چه طول وابعادی مناسب می باشد؟
در روش چاپ دستی کوچک ترین طول حرارتی مناسب می باشد اما اگر از ماشین چاپ استفاده میشود تعداد تولیدات در ساعت ماشین چاپ تعیین کننده طول وابعاد درایر می باشد .
معمولا حد اکثر سرعت های درایرها 6 متر در دقیقه می باشد .
محاسبه طول درایر از جدول زیر قابل محاسبه می باشد
اگر طول ابعاد یک تیشرت 60 سانتیمترباشد طول حرارتی درایر 6 متر باشد و سرعت درایر 6 متر در دقیقه باشد این درایر میتواند حداکثر10 عدد تیشرت در دقیقه خروجی داشته باشد (600 عدد در ساعت ) که زمان پخت (Curing time ) هر تیشرت 1 دقیقه میباشد حال اگر نیاز به 2 دقیقه زمان پخت را داشته باشیم سرعت درایر باید 3 متر در دقیقه باشد. که خروجی آن 300 عدد در ساعت می باشد.حال محاسبه کنید Curing Information یک نوع رنگ را 160 درجه 3 تا 5 دقیقه که با سرعت 3 دقیقه 200 عدد در ساعت وبا سرعت 5 دقیقه 120 عدد در ساعت خروجی خواهیم داشت .
به همین روش می توان طول حرارتی مناسب را با توجه به سرعت ماشین چاپ انتخاب نمود در جایی که امکان طول وجود نداشته باشد می توان عرض بیشتر مد نظر باشد.
در حال حاضر مناسب ترین نوع درایر به دو عامل اصلی بستگی دارد :
- مصرف کم انرژی بطوری که برای هر 150 ساتیمتر طول حرارتی با عرض 80 ساتیمتر در نوع برقی حداکثر 3 کیلو وات مصرف در ساعت
- انتقال حرارت به روش هوای گرم
تالیف : مهندس علیرضا مقدم